Discover What is Porosity in Welding and Its Result on Structural Integrity
Discover What is Porosity in Welding and Its Result on Structural Integrity
Blog Article
The Scientific Research Behind Porosity: A Comprehensive Overview for Welders and Fabricators
Understanding the elaborate devices behind porosity in welding is crucial for welders and fabricators aiming for flawless workmanship. From the make-up of the base products to the intricacies of the welding process itself, a plethora of variables conspire to either aggravate or alleviate the presence of porosity.
Understanding Porosity in Welding
FIRST SENTENCE:
Evaluation of porosity in welding exposes important understandings right into the stability and quality of the weld joint. Porosity, characterized by the presence of dental caries or gaps within the weld steel, is an usual worry in welding processes. These voids, if not effectively resolved, can jeopardize the structural honesty and mechanical residential or commercial properties of the weld, resulting in potential failures in the finished product.

To detect and evaluate porosity, non-destructive screening approaches such as ultrasonic screening or X-ray examination are commonly utilized. These techniques permit the identification of inner flaws without jeopardizing the stability of the weld. By analyzing the dimension, shape, and circulation of porosity within a weld, welders can make educated decisions to boost their welding procedures and accomplish sounder weld joints.
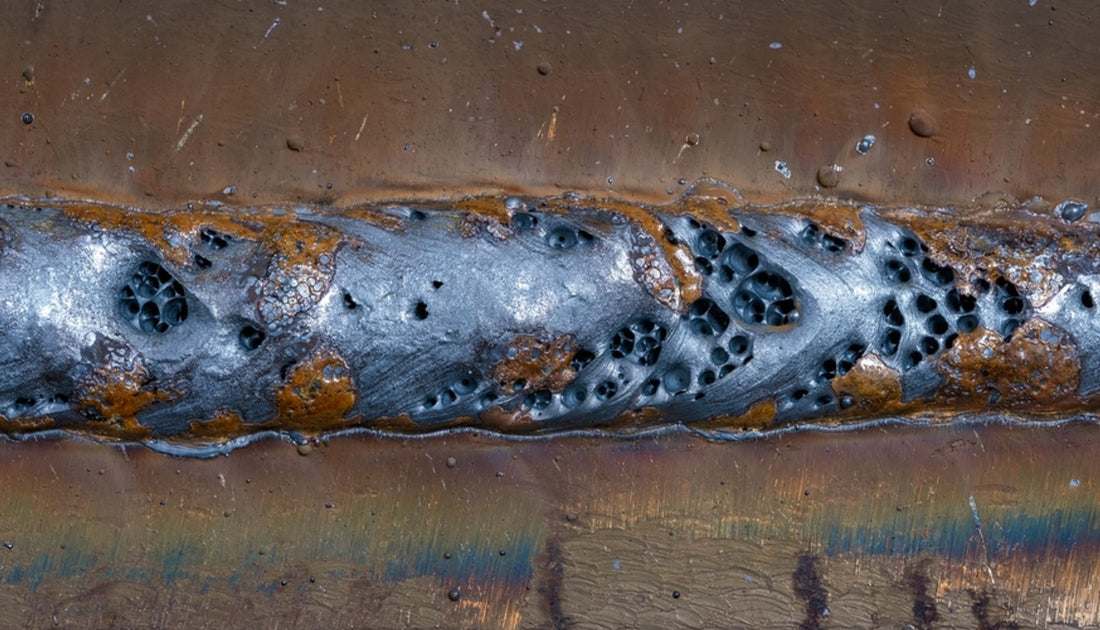
Aspects Influencing Porosity Formation
The event of porosity in welding is affected by a myriad of variables, ranging from gas shielding effectiveness to the intricacies of welding specification settings. One vital variable contributing to porosity formation is poor gas protecting. When the protecting gas, typically argon or carbon dioxide, is not successfully covering the weld swimming pool, atmospheric gases like oxygen and nitrogen can pollute the molten metal, bring about porosity. Additionally, the sanitation of the base products plays a considerable role. Impurities such as corrosion, oil, or wetness can vaporize throughout welding, producing gas pockets within the weld. Welding parameters, consisting of voltage, current, take a trip speed, and electrode kind, also influence porosity formation. Making use of incorrect settings can produce excessive spatter or warm input, which in turn can result in porosity. The welding strategy employed, such as gas steel arc welding (GMAW) or shielded metal arc welding (SMAW), can affect porosity formation due to variants in warm distribution and gas protection. Recognizing and managing these variables are important for decreasing porosity in welding operations.
Effects of Porosity on Weld High Quality
The existence of Full Report porosity also deteriorates the weld's resistance to rust, as the entraped air or gases within the spaces can respond with the surrounding atmosphere, leading to destruction over time. Additionally, porosity can impede the weld's ability to stand up to stress or impact, further endangering the overall quality and reliability of the bonded framework. In crucial applications such as aerospace, automotive, or structural buildings, where safety and longevity are paramount, the damaging results of porosity on weld top quality can have extreme consequences, emphasizing the relevance of lessening porosity via proper welding methods and procedures.
Methods to Lessen Porosity
To boost the high quality of bonded joints and make sure structural stability, welders and fabricators use details strategies targeted at minimizing the development of gaps and dental caries within the material throughout the welding process. One reliable technique to decrease porosity is to why not try here make sure proper material prep work. This includes comprehensive cleaning of the base metal to get rid of any pollutants such as oil, grease, or wetness that can contribute to porosity development. see Furthermore, using the suitable welding specifications, such as the proper voltage, present, and take a trip rate, is essential in stopping porosity. Preserving a regular arc size and angle during welding likewise helps in reducing the chance of porosity.

Moreover, picking the appropriate securing gas and keeping appropriate gas circulation prices are crucial in decreasing porosity. Making use of the appropriate welding method, such as back-stepping or utilizing a weaving motion, can additionally aid disperse warm uniformly and decrease the chances of porosity formation. Finally, making sure proper ventilation in the welding environment to get rid of any kind of possible resources of contamination is important for accomplishing porosity-free welds. By executing these techniques, welders can effectively reduce porosity and create premium welded joints.

Advanced Solutions for Porosity Control
Executing cutting-edge modern technologies and ingenious methods plays an essential role in attaining remarkable control over porosity in welding processes. In addition, using sophisticated welding strategies such as pulsed MIG welding or customized atmosphere welding can likewise help alleviate porosity issues.
One more advanced option entails making use of innovative welding equipment. For circumstances, utilizing devices with integrated attributes like waveform control and innovative source of power can improve weld quality and reduce porosity threats. The execution of automated welding systems with precise control over parameters can dramatically lessen porosity issues.
Furthermore, including innovative surveillance and inspection technologies such as real-time X-ray imaging or automated ultrasonic screening can assist in detecting porosity early in the welding procedure, permitting for instant rehabilitative activities. Overall, integrating these sophisticated options can substantially boost porosity control and boost the overall top quality of welded components.
Conclusion
In conclusion, comprehending the science behind porosity in welding is necessary for welders and makers to create premium welds. By determining the variables influencing porosity formation and implementing techniques to minimize it, welders can improve the overall weld quality. Advanced solutions for porosity control can additionally boost the welding process and ensure a strong and reliable weld. It is very important for welders to continuously educate themselves on porosity and apply ideal practices to accomplish optimal results.
Report this page